A few decades ago, yogurt was just another minor food product, enjoyed by a small minority of people. How times have changed! Since the 1980s, yogurt’s popularity has increased five times over, and today it’s one of the most popular foods in the world.
According to statista.com, the global yogurt market reached 168 billion USD in 2023, and it’s projected to keep growing by more than seven percent a year through at least 2028. It’s a worldwide business too, with the Asia Pacifica region the biggest consumer of all.
Yogurt’s popularity is not hard to understand. It’s seen as both a healthy and nutritious food, as well as a delicious snack. All of this makes the yogurt industry very competitive, and in a market where consumers are focused on health, any improvement in safety is an important advantage.
That’s why yogurt makers and OEMs who service that market are starting to adopt XENON Pulsed Light for one of the crucial safety steps in yogurt production: pre-fill sterilization.
The FCM30-L4 Ultra-Clean Fill-Seal Machine produced by Alfa Machine incorporates XENON Pulsed-UV technology, providing in-line decontamination of cups and soft lids. See video.
Better safety, fewer problems
Pre-fill sterilization in food packaging, especially for products like yogurt, is crucial for eliminating harmful microbes, ensuring product safety, extending shelf life, and maintaining quality.
Traditionally, yogurt producers have used chemicals or heat to sterilize cups before filling, but these approaches have drawbacks. Chemicals can leave residue and pose a disposal hazard. Heating has drawbacks too, such as slowing down production and/or limiting the materials that can be used.
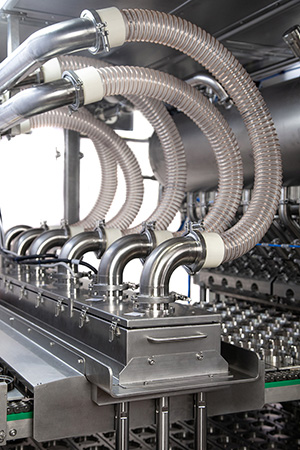
XENON pulsed UV lamp housings are installed in-line for continuous yogurt cup and lid decontamination.
XENON Pulsed Light is a big improvement on these processes. A chemical-free approach, it works by producing brief, intense bursts of broad-spectrum light, including ultraviolet (UV) light, that destroys virtually all known pathogens in only a few seconds or less.
Research and practice have proven this technology to be highly effective, and much faster than other methods. What’s more, Pulsed Light produces little or no heat, so it can be used with most package materials, including plastic, bottles, and glass. And, it’s approved by the FDA for use with foods.
Will it disrupt existing processes and production lines?
While you might think introducing new technology into the production line would be disrupting, that’s not the case with XENON Pulsed Light.
The systems are flexible and easy to install in various parts of the manufacturing process, such as filler machine lines or conveyor systems, and can come with food-grade wash-down lamp housings. Different lamp configurations allow the system to be adapted to most wide-mouth containers.
“Protected by XENON PurePulse™ technology”
In a world where people are focused on health and safety, safer packaging can be a big competitive advantage. In the yogurt industry especially, why not offer the best pre-fill sterilization practice available? Employing a cutting-edge and eco-friendly sanitization method like Pulsed Light can enhance a brand’s reputation, appealing to health-conscious and environmentally aware consumers.
If you are a yogurt producer or an OEM interested in yogurt safety, XENON would like to hear from you. Some OEMs have already begun offering solutions based on XENON PurePulse™ technology. For instance, Alfa Machine, a leader in food packaging, has added XENON Pulsed Light to its solution set for the yogurt industry.
Why not your company? To learn more about this important new application in food safety, please contact XENON today.